Building Affordability by Building Affordably: Exploring the Benefits, Barriers, and Breakthroughs Needed to Scale Off-Site Multifamily Construction
Published On March 7, 2017
To remain relevant and successful over time, every industry must modernize and adapt to changing demands and opportunities in the marketplace. The housing development industry is no exception, and over the years, has experienced its fair share of evolutions and revolutions in business model and product design. Today, as housing developers face rapidly changing consumer preferences, population demands, technological advances, and an ever- rising cost of construction, the adage “innovate or perish” may be timelier than ever.
How will the housing industry adapt to these new realities? As a recently released report from McKinsey & Company points out, the construction sector is especially ripe, or better said, overdue, for an infusion of innovation. Inefficiencies in traditional construction have hampered productivity and driven costs up for decades, resulting in increasingly costly development. Today, in many regions in the United States, the production of housing – especially infill multifamily housing – has become so costly to produce it demands rents or sale prices that are unaffordable for most people. While the cost of construction is not the only reason housing prices continue to increase, they are certainly a major factor.

Off-site construction of housing, which leverages the efficiencies of factory production to achieve significant cost savings, represents a much needed solution to this problem. It has the potential to revolutionize the way homes and apartments are built.
Producing housing off-site involves manufacturing modules or components of a unit in a factory, and then transporting these to lots for installation and stacking in a process akin to interlocking Lego blocks. This method is sometimes referred to as modular or prefab development, though there are technical differences. With up to a 50 percent shorter production time and up to 20 percent savings on construction costs alone, off-site construction methods allow for more housing to be produced more quickly at a lower price. The potential result of this innovation at scale? Lower rents and home prices for millions of American families currently burdened by high costs of housing.
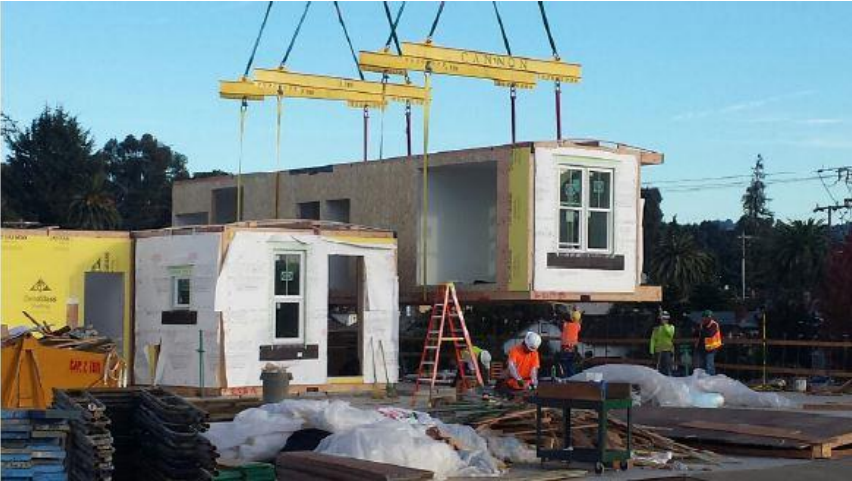
While a number of other countries such as Sweden have already broadly integrated off-site construction, only a few off-site factories are currently in operation in the United States. Today, the Terner Center is releasing a new paper exploring the benefits, barriers, and breakthroughs needed to significantly expand this construction method in the American market, particularly in the multifamily development sector. The paper documents the potential cost savings, time savings and other benefits of off-site construction, identifies some of the key reasons it hasn’t yet taken off, and puts forth several ideas for how to overcome these challenges to bring it to scale.
Solving the complex housing affordability challenges facing many high-cost regions in the United States is ultimately going to require innovation and leadership from all sectors. Local land use policy decisions, state approvals processes, and federal housing expenditures are all important, but just as essential is the willingness and audacity of private sector leaders to work through the complexity of innovation and bring good ideas like off-site multifamily construction to scale. As a business opportunity and a pathway to addressing the growing lack of affordability in the United States housing market, there is much to be gained by expanding the practice of off-site construction. The time is now for the industry to take this leap forward.